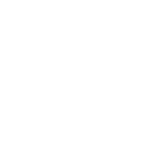
360° Services
MEDICAL DEVICE
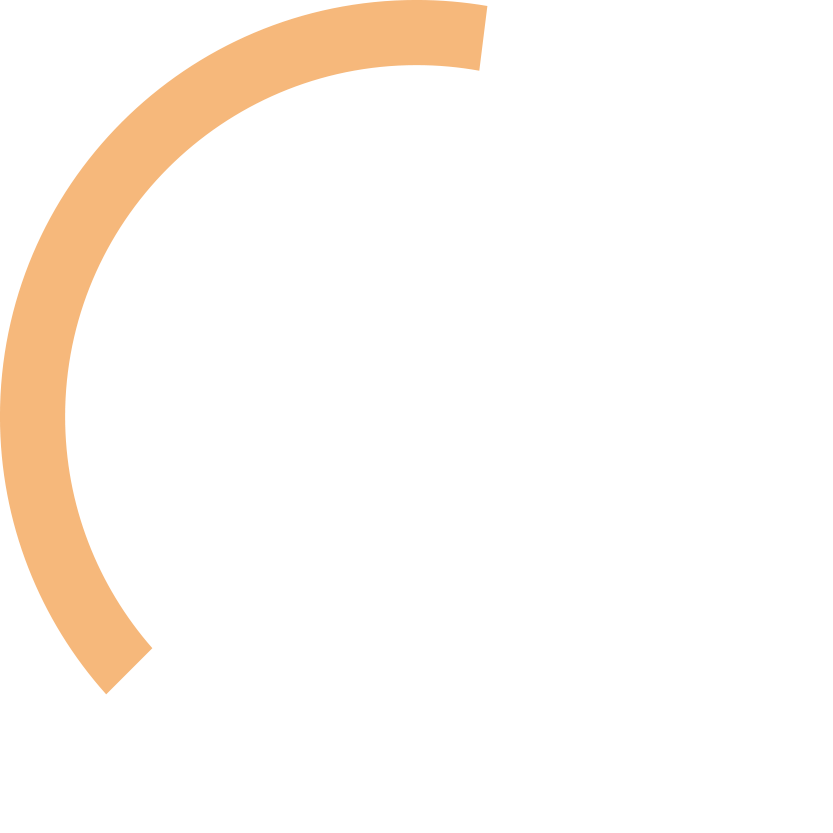
Design
The technical office provides customers with assistance and engineering consultancy for the development of any product, suggesting different technical solutions. Starting from the study of the project together with the customer, we move on to the testing phase with the creation of prototypes and their validation, up to the release of the final technical drawing.
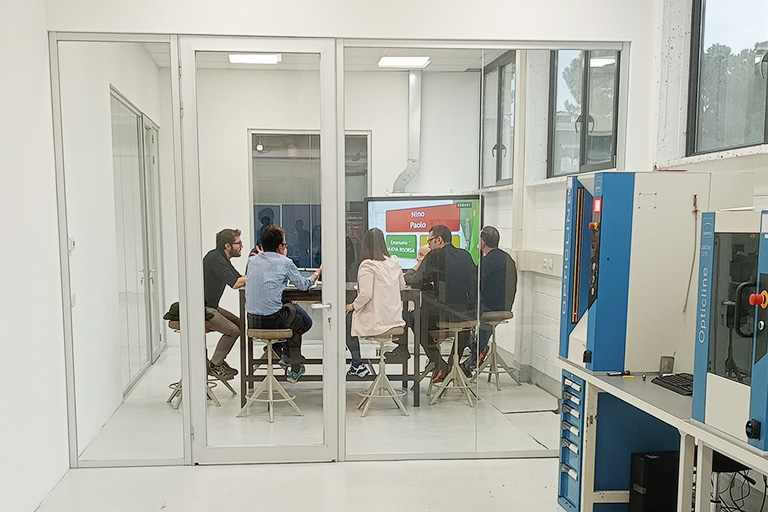
01
Startup
Startup of the project in collaboration with the client:
- pre-specifications
- patent analysis
- preliminary risk analysis
- requirements identification
- project plan drawing up
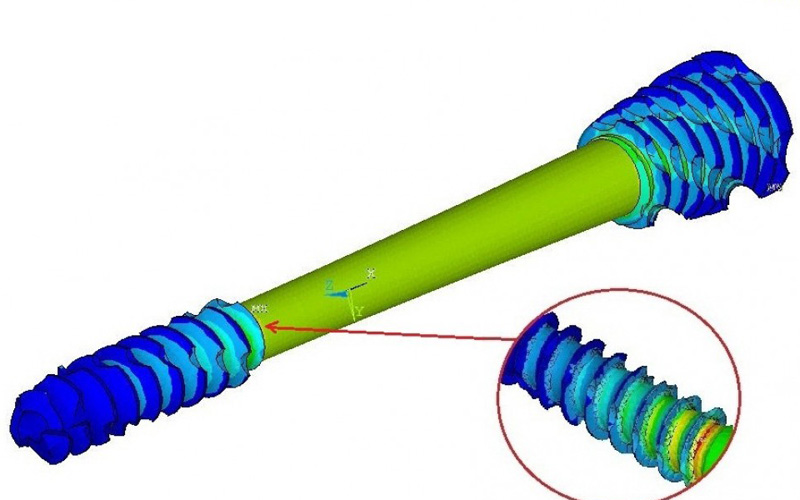
02
Test
- prototypes realization
- statistic tests
- fatigue tests
- clinical trials
- osteo-integration tests
- research on packaging materials
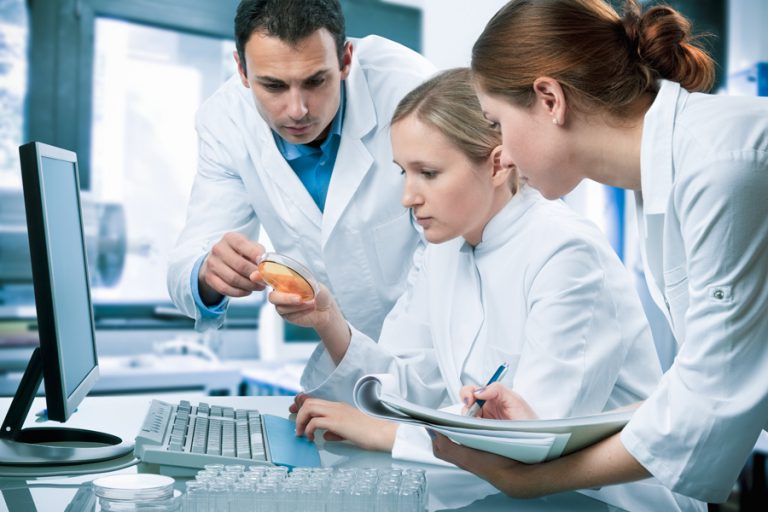
03
Validation
- chemical cleaning validation
- biological cleaning validation
- biocompatibility validation
- sterilization cycle validation
- packaging validation
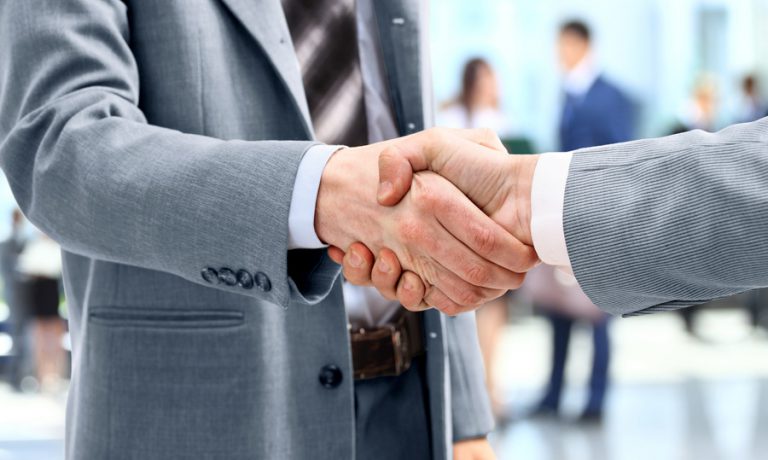
04
Project approval
- final technical drawings
- final plans and control cycle
- final product specification
- project validation
- technical file drafting
- CE Mark
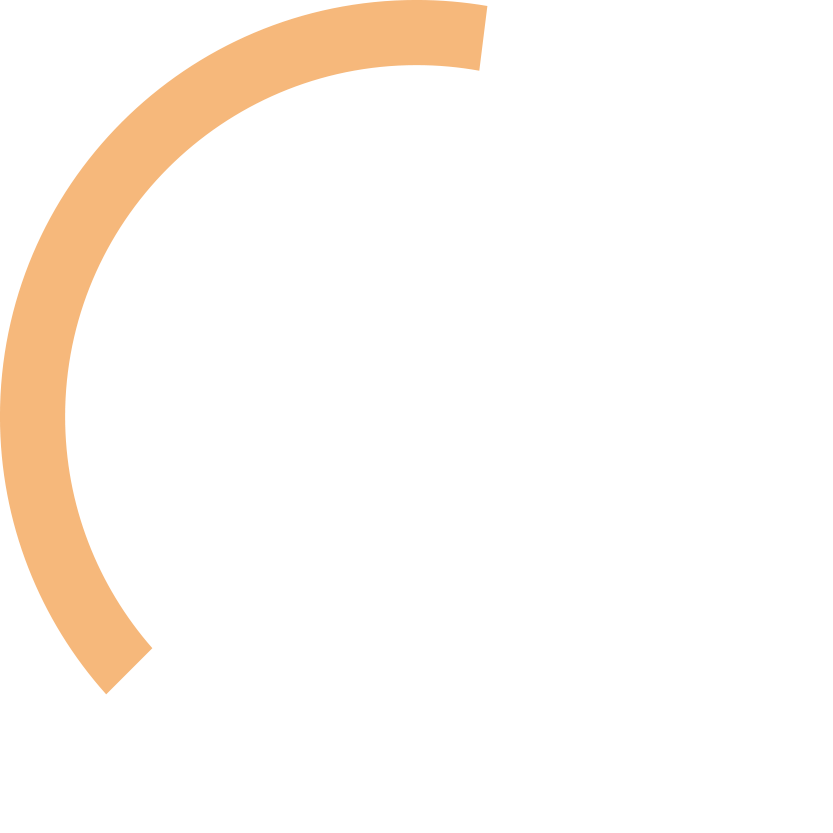
Cad-Cam
The creation of each new medical device is processed using Cad-Cam software, starting from the 3D files supplied by customers. These software can simulate the operations of the processing phase thanks to various parameters. This allows to evaluate the most critical aspects of the processes and to define the most suitable solutions.
CAD-CAM
When the use of a 5-axis machining center is required for the creation of the medical device, the various processes to be performed are evaluated by importing the customer’s three-dimensional files into a CAD-CAM software. Thanks to these software it is possible to evaluate all the production phases on video, by entering the various parameters necessary for the simulation of the processes.
These simulations allow to evaluate in advance the most critical aspects of the processes and to find suitable solutions for production. All at a much lower cost.
QUALITY AT RIGHT PRICE
These software are also very important to evaluate different ways of making the device. Generally, several solutions are tried until the most suitable one is found, to the full advantage of production times and therefore costs.
Only thanks to the experience of our operators, it is possible to go further and further in the search for simple and economical solutions, without renouncing the quality of the particular products.
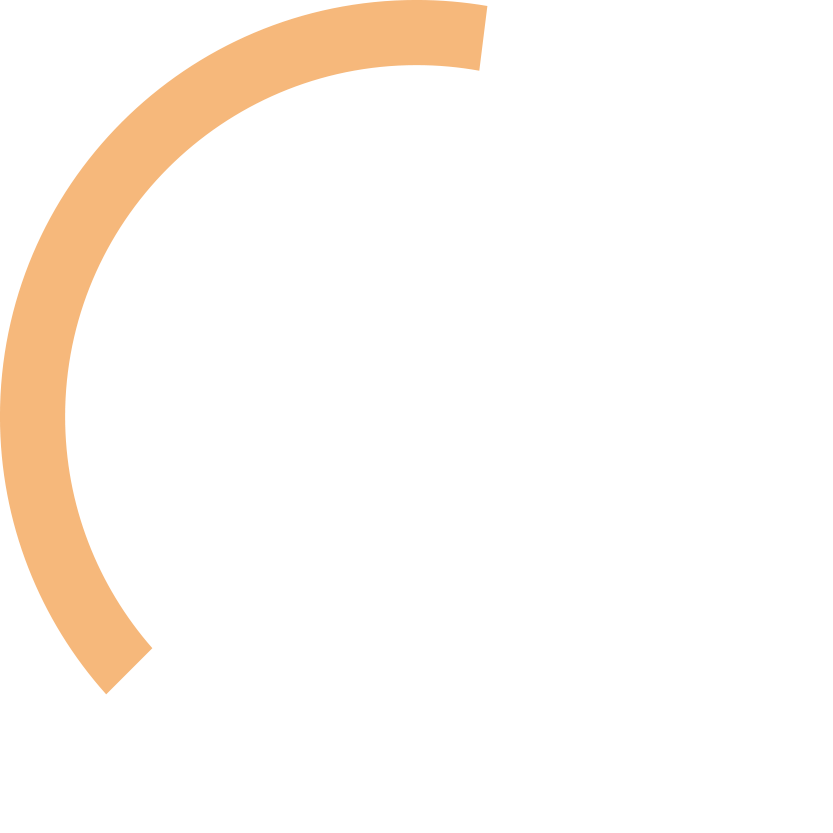
Production
Thanks to our machinery department which we annually implement and update, we are able to create various products that differ in material and production technology (Swiss type lathe, 5-axis machining centres, injection and compression plastic molding).
02
5 axis milling center
All the components that require very high precision machining, which are not feasible for turning, are made on the eight 5 axis milling centers, equipped with high frequency spindles.
We have chosen to equipe these machines with robots. This has allowed us to increase the production rate without sacrificing the quality of the products and reducing the costs.
We are able to work the following materials: titanium (all grades), cobalt chrome, AISI 316/316L, aluminum, AISI430.
03
Plastic injection molding and compression molding
Thanks to a series of hydraulic presses, with a maximum capacity of 45 tons, we are able to produce various types of products in different materials. Molding takes place in the ISO 7 area.
The advanced molding technology allows the realization of complex parts to be produced in large volumes and with limited costs.
All the raw materials used such as polyethylene, CFR Peek, Radel, PLDL, PLLA comply with the medical industry regulations.
All products are identified with laser marking, in order to maintain product traceability.
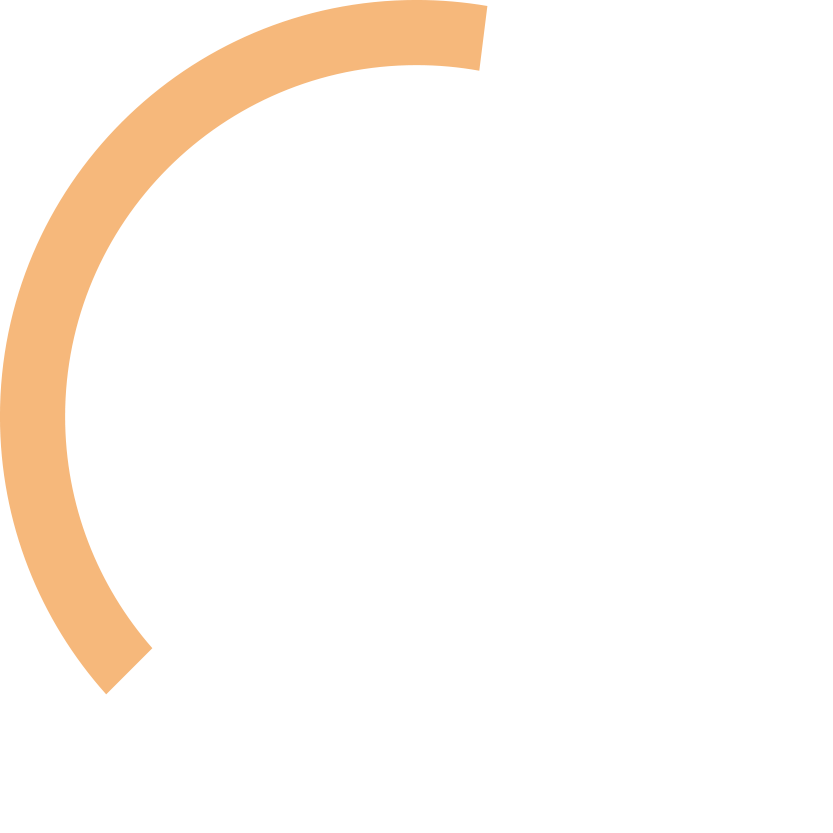
Finishing
We provide customers with any type of finishing, such as for example tumbling, sandblasting, electro polishing, manual polishing, anodizing, laser marking, etc.
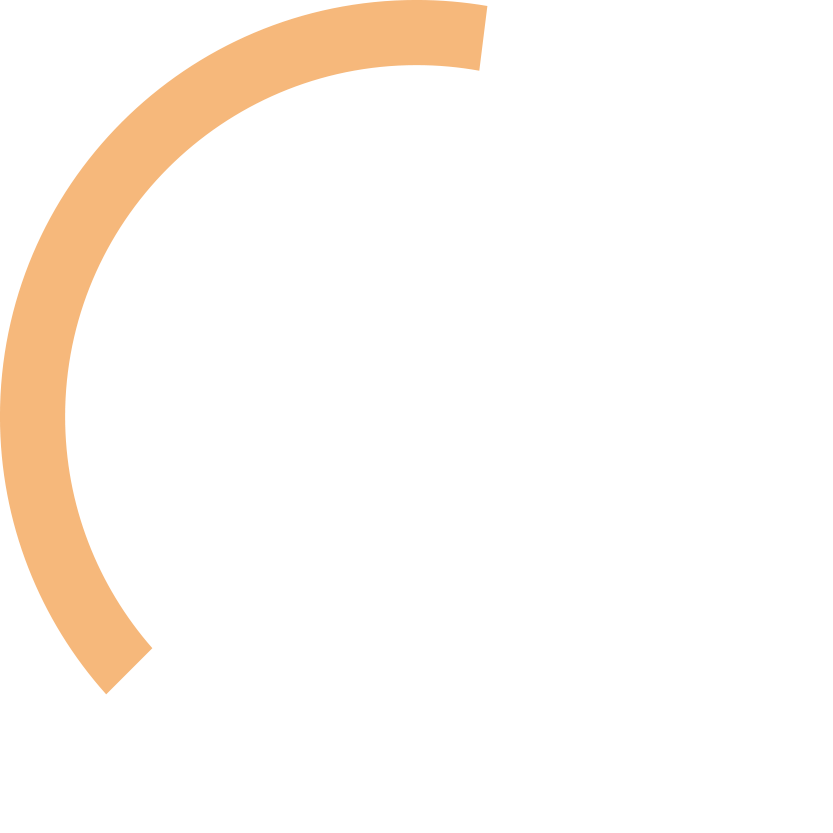
Cleaning
At the end of the production process, the medical devices are subjected to cleaning systems in decontaminated water to guarantee the maximum possible cleanliness of the component before the final packaging in clean room. Our department makes use of validated and certified systems, with a high level of automation, in order to guarantee the level of biobarden required by the customer.
01
Packaging
After the check, the product is sent for packaging according to validated procedures.
Packaging for sterile products takes place in clean rooms ISO 7 and ISO 8.
Inside, in controlled atmosphere conditions, ultrasonic cleaning and drying of the various components are carried out by specialized personnel.
This phase is followed by primary packaging (blister packs, tyvek bags or vacuum bags) which guarantees perfect seal against external pollutants.
The packaging work is perfected with the labeling and the insertion of the blisters in the special boxes that are protected from dust by a transparent heat-shrink film.
Once the operation is completed, the products are sent for sterilization with cycles validated by external suppliers.
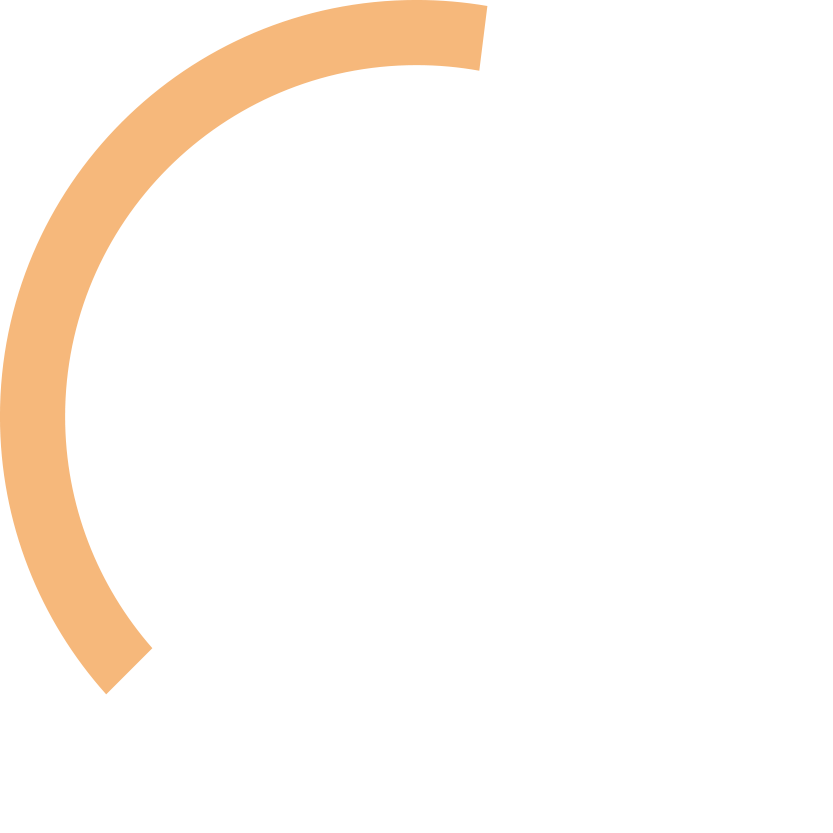
VMI System
Market needs don’t very often correspond to the production times of medical devices. To overcome these problems, our company has the so called VMI System (vendor managed inventory) service which allows the control, planning and management of stocks of the customer.
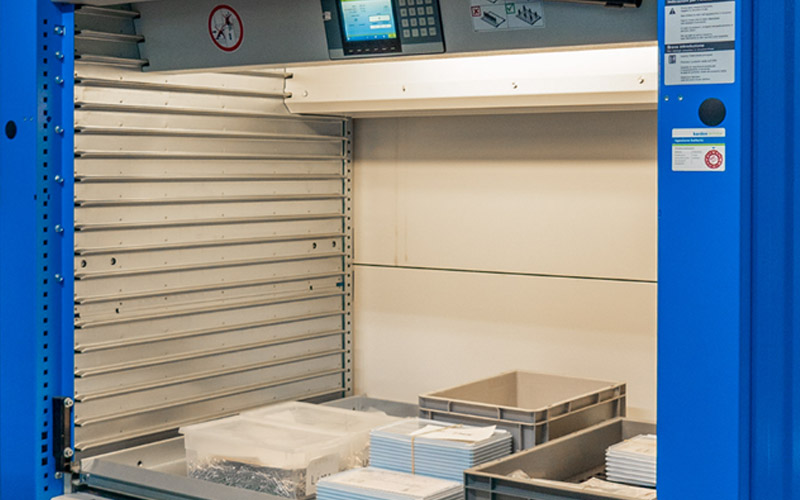
01
Automatic warehouses
The management of finished products is very importante like the one of raw materials. For this reason we have equipped with automatic vertical warehouses. This choiceis important to provide our customers with the possibility of stocking up on components in the warehouse for them. This secures them from possible production delays and, moreover, facilitates them on the market. They are in fact aware of having a always available supply.